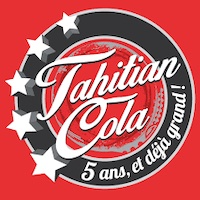
New air conveyor line
New air conveyor line for bottles at Pacific Drinks in Tahiti
Current situation
- Manual arrangement of bottles on the bottling line
- Workshop clutter and major ergonomic problems
Objectives
- Automate the blow-moulder/filler connection
- Facilitating forklift traffic
Our customer, concerned about the quality and well-being of its employees, was looking to integrate its 1BLOW blower from its air conveyor into a CIMEC filling unit. However, the major challenge was to maintain a fluid flow between these machines despite a distance of just a few meters.
Faced with this situation, sending a technician to carry out a dimension survey on site in Tahiti proved uneconomical. That's why, in collaboration with a local architectural firm, we opted for an innovative approach: a 3D scan of the building was taken, then sent to ACCS Packaging for 3D processing. This enabled us to design a compact, ergonomic solution that fully satisfied our customer.
The layout of the air conveyor was meticulously validated using a 3D simulation on SolidWorks. After design, the material was shipped by sea to Tahiti. To guarantee the versatility required by our customer, we recommended the use of our UBIC guidance system, enabling us to handle all existing and future formats without the need for mechanical modifications.
With a view to minimizing travel costs, we sent a small team to the site: a head mechanical fitter, assisted by a local team, managed to assemble the new air conveyor line in just three weeks. At the same time, an automation specialist took charge of commissioning the program and operator interface in just over a week, taking the time needed to anticipate and resolve all possible scenarios.
Your project starts here!
ACCS PACKAGING
771 Allée de la Baraquette
30390 DOMAZAN
France
Opening hours
Monday to Friday: 9 a.m. to 6 p.m.
Phone
(+33) (0)4 66 01 37 48