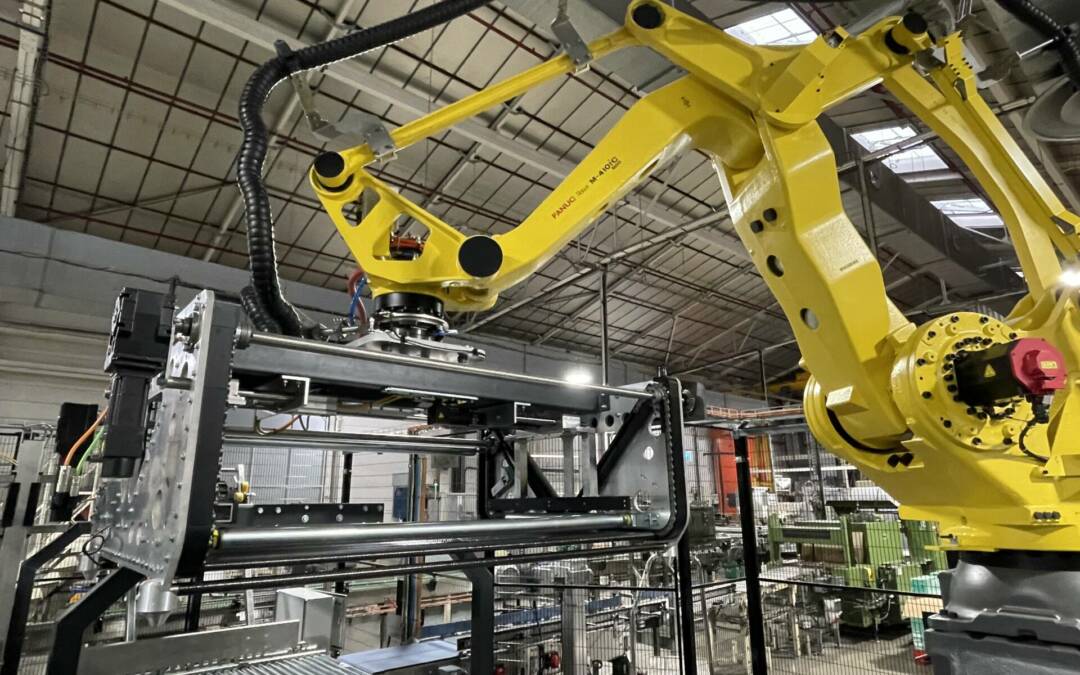
New Raynal et Roquelaure palletizing robot
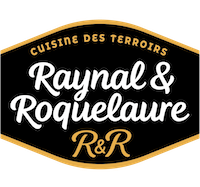
New palletizing robot
New palletizer at Raynal et Roquelaure
Current situation
- Obsolescence of existing palletizer
- High failure rate
- Existing equipment not suitable for small tray production
Objectives
- Install a robot for palletizing all bundle formats
- Increase output by 30%.
- Improving the man-machine interface
As part of our commitment to improving our customers' efficiency and productivity, ACCS Packaging recently undertook a project to replace an aging Cartesian palletizer with an advanced palletizing robot. The specifications were complex: the palletizing rate had to be increased by 30% to anticipate the integration of new machines, while incorporating formats usually palletized manually.
To meet this challenge, ACCS Packaging, in collaboration with its partner INSARhas developed an innovative solution incorporating a robot with two removable heads, enabling small and large loads to be handled separately:
- for small loads, a gripper head equipped with a diaper suction system is used.
- for larger loads, a larger dismountable head equipped with two retractable curtains is used. The rollers of this head are made of carbon/kevlar, guaranteeing rigidity and lightness.
Considerable design effort was devoted tooptimizing the machine's infeeds, thus reducing layer preparation cycle times. ACCS Packaging and INSAR also supplied all the conveyors for bundles and pallets, ensuring a complete, integrated solution.
The project was implemented by INSAR in just 4 weeks. The customer expressed great satisfaction with the quality of the equipment installed, as well as with the competence and professionalism of the engineers and technicians involved in the project.
This success illustrates our ability to provide innovative and efficient palletizing solutions, meeting the specific needs of each customer while improving their productivity and operational efficiency.
Your project starts here!
ACCS PACKAGING
771 Allée de la Baraquette
30390 DOMAZAN
France
Opening hours
Monday to Friday: 9 a.m. to 6 p.m.
Phone
(+33) (0)4 66 01 37 48